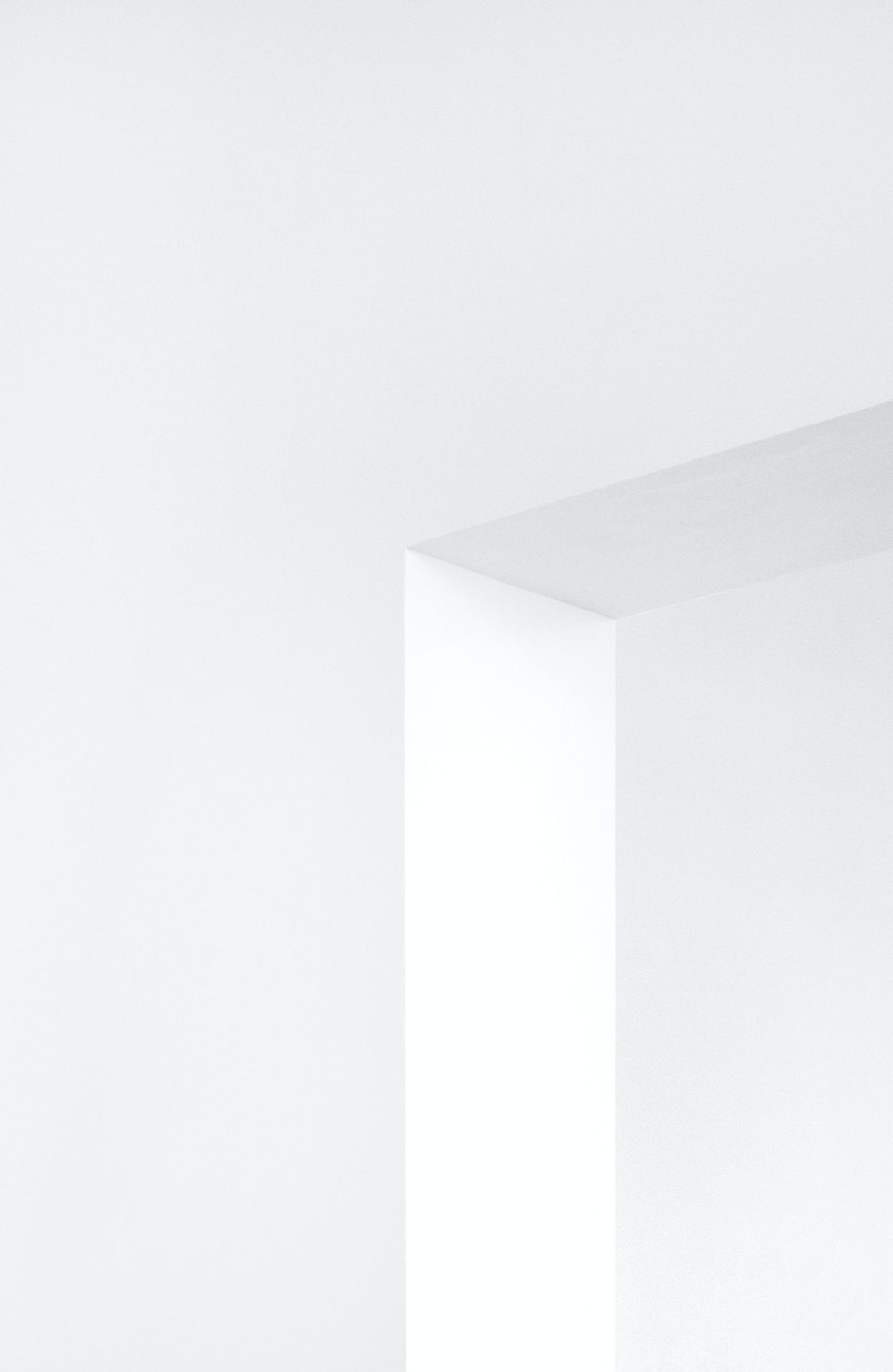
CNC Machining

Nanobubbles in CNC Machining: Precision, Cooling, and Lubrication for Optimal Performance
CNC (Computer Numerical Control) machining is essential for creating high-precision components used in industries such as aerospace, automotive, and medical devices. However, CNC machining processes generate substantial heat and friction, necessitating efficient cooling and lubrication to maintain part accuracy, reduce tool wear, and prevent material degradation. Nanobubble technology offers a game-changing approach to cooling and lubrication, providing highly effective, resource-efficient solutions that support cleaner and more sustainable CNC operations. This blog explores how nanobubbles are transforming CNC machining and improving performance.
Challenges in CNC Machining Cooling and Lubrication
Key challenges in CNC machining include:
-
Heat Buildup: High-speed cutting generates significant heat, which can damage parts, cause accuracy issues, and wear down tools.
-
Effective Lubrication: Proper lubrication is essential to reduce friction and prevent damage to both the tool and workpiece.
-
Coolant Waste: Conventional coolant and lubricant solutions often create waste and require disposal, which is both costly and environmentally harmful.
Nanobubbles bring unique cooling and lubrication capabilities, addressing these challenges while supporting sustainable machining practices.
How Nanobubbles Benefit CNC Machining
Nanobubbles provide precise cooling and lubrication benefits that enhance the CNC machining process:
-
Enhanced Cooling Efficiency: Nanobubbles improve the heat absorption capacity of water-based coolants. The tiny bubbles increase the surface area, allowing for more efficient heat dissipation. This prevents overheating, maintaining tool sharpness and part accuracy.
-
Improved Lubrication: When infused with lubricating agents, nanobubbles deliver a consistent, uniform lubricant film over the tool and workpiece. This reduces friction, minimizes wear, and extends tool life, all while maintaining high precision during machining.
-
Reduced Coolant Waste: Nanobubbles help optimize coolant use, reducing the volume required and lowering disposal costs. Their stability allows for extended coolant life, which is both cost-effective and environmentally friendly.
-
Surface Finish Improvement: Nanobubbles create a smoother coolant and lubricant layer, which helps achieve a finer surface finish on machined parts, reducing the need for secondary finishing processes.
Applications of Nanobubbles in CNC Machining
Nanobubbles can be used across various CNC machining processes, including:
-
Milling and Drilling: In high-speed milling and drilling operations, nanobubbles reduce the thermal load on tools, ensuring optimal cutting performance and tool longevity.
-
Grinding and Polishing: For grinding and polishing applications, nanobubble-infused coolants enhance surface finish quality by providing consistent cooling and lubrication, leading to smoother results.
-
Turning and Lathing: Nanobubbles reduce friction and heat in turning operations, improving precision and extending the life of cutting tools, which is particularly valuable in high-volume manufacturing.
Case Studies and Results
Several CNC machining facilities have adopted nanobubble technology, seeing significant performance improvements:
-
Extended Tool Life: In one case, a CNC facility using nanobubble coolants observed a 30% increase in tool lifespan due to improved cooling and lubrication, resulting in lower tool replacement costs.
-
Higher Part Accuracy in Aerospace Manufacturing: An aerospace manufacturer incorporated nanobubble-infused lubricants, achieving higher dimensional accuracy and a finer surface finish, reducing the need for secondary finishing processes.
-
Reduced Coolant Usage: A machine shop reported a 25% reduction in coolant volume and disposal costs by switching to nanobubble-enhanced coolants, contributing to overall cost savings and reduced environmental impact.
Conclusion: Precision and Sustainability for Modern Machining
Nanobubbles offer CNC machining a sustainable, high-performance alternative to traditional cooling and lubrication methods. With improved tool life, higher part accuracy, and reduced waste, nanobubbles support more precise, efficient, and environmentally friendly machining processes. As the manufacturing industry moves toward cleaner and more resource-efficient practices, nanobubbles will continue to play a transformative role in advanced machining technologies.